Storage Location
Introduction/Purpose:
In a procurement system, the storage location refers to the physical or virtual location where goods or materials are stored before they are used or distributed. It is an essential aspect of inventory management and plays a crucial role in the overall procurement process. The storage location serves as a central hub for receiving, storing, and tracking inventory items within an organization.
The storage location in a procurement system is typically synchronized with the organization’s inventory system or warehouse master. This synchronization ensures that the procurement system has up-to-date information about the storage locations available. The warehouse master contains details such as the type of storage (e.g., racks, bins, shelves), the physical location, contact person details, and the purpose of the storage (whether it is for internal use, external use, or both).
The storage location allows for efficient storage and retrieval of inventory items. It helps in organizing the inventory based on specific criteria, making it easier for employees to locate and retrieve items when needed. This minimizes search times, reduces errors, and enhances overall operational efficiency within the procurement system.
In summary, the storage location in a procurement system serves as a central hub for managing inventory items. It ensures efficient storage, accurate tracking, and timely distribution. By synchronizing storage locations from the inventory system or warehouse master, organizations can optimize their supply chain, streamline operations, and support the overall success of their procurement activities.
Dependency:
Here are the key dependencies for recording storage location masters:
- Inventory Management System: The procurement system should have an integrated inventory management module that supports recording and managing storage location information. The storage location master data will be stored and accessed within this module.
- Inventory Classification and Categorization: The storage location master data should consider the classification and categorization of inventory items. Different storage locations may be created based on factors such as product type, category, size, or specific handling requirements. The storage location master should support the assignment of inventory items to the appropriate storage locations.
By considering these dependencies, organizations can effectively record the storage location master in their procurement system. This ensures that accurate and relevant information about storage locations is available for efficient inventory management, smooth receiving and distribution processes, and informed decision-making.
How To Navigate:
The navigation to record a Storage Location in a procurement system typically involves the following steps:
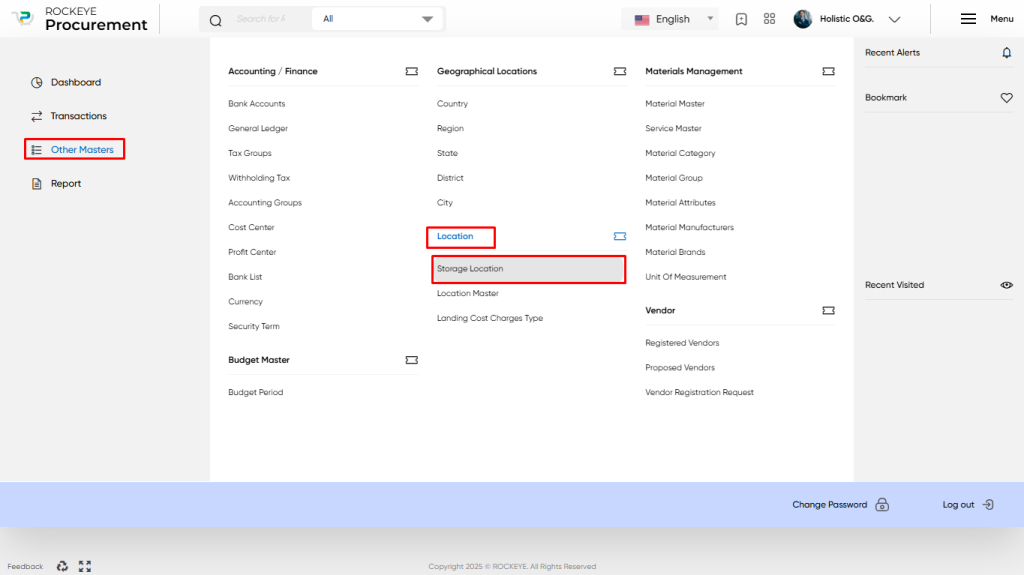
- Click on the main navigation icon: The main navigation icon may be located in the top right corner of the screen. Clicking on this icon will open the navigation menu, which typically includes links to various sections of the procurement system.
- Click on the Other Master section: The Other Master section is located under the left section of the screen; clicking on this section will display a list of other masters related to procuring.
- Find the Location section: The Location section is located in the list of Master under the Master section. Clicking on this section will display a list of masters related to location.
- Click on the Storage Location link: The Storage Location link is located under the Location section. After clicking on this link, you can navigate to Storage Location in the listing, and from that, you can easily upload new transactions into the system.
Listing:
In a procurement system, the storage location listing provides a comprehensive view of the storage locations available within the organisation. Here are the key features and options typically included in a storage location listing:
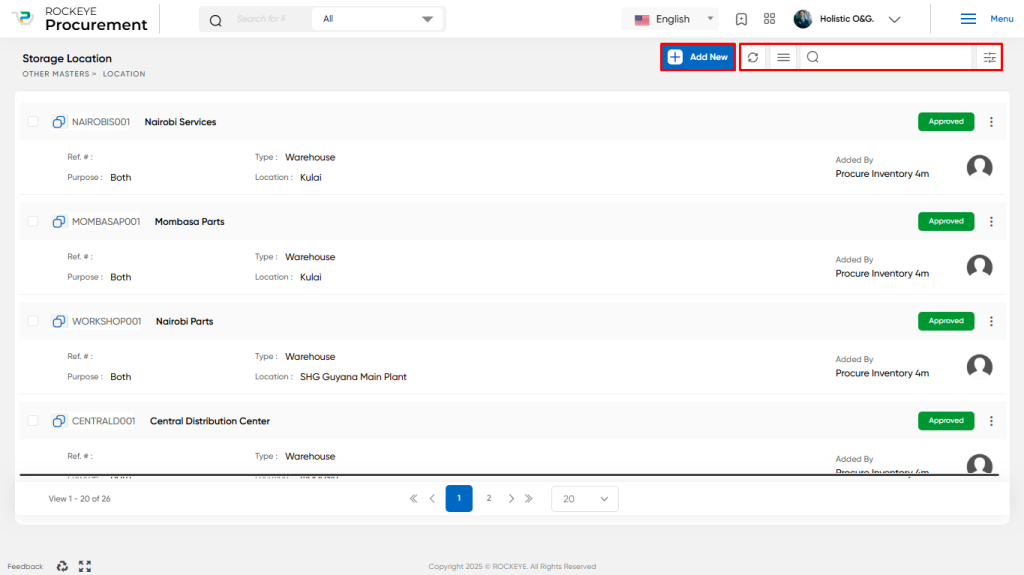
- Show All: This option displays all the latest refreshed records of storage locations. It provides an overview of all the storage locations currently recorded in the procurement system.
- Extra Options:
- Export: Allows users to export the storage location listing to a file format such as Excel or CSV for further analysis or reporting purposes.
- Columns: Provides the ability to customise the columns displayed in the storage location listing. Users can choose specific attributes or data fields to be included in the view.
- Search: Enables users to set search conditions or criteria to filter the storage location listing based on specific attributes or values.
- Sync with Inventory: This option allows users to synchronise the storage location data with the organisation’s inventory system or warehouse master, ensuring that the listing remains up-to-date.
- Filter: The filter option allows users to apply filters to the storage location listing based on specific conditions. This enables users to narrow down the displayed records and focus on specific storage locations that meet certain criteria, such as location, storage type, or usage purpose.
- Search: Users can perform a search within the storage location listing to find specific records or information. The search functionality enables users to search for keywords or values across all records, making it easier to locate specific storage locations or related information.
- Card View Listing: The storage location listing will get displayed in a card view format, where each storage location is represented as a card with key information. The key information typically includes the storage location name, code, usage purpose, type of storage location, location details, the user who added the record, approval status, and other options such as an activity log.
The storage location listing in a procurement system provides a centralised view of all the storage locations within an organisation. It allows users to access, manage, and analyse storage location data, facilitating efficient inventory management, informed decision-making, and streamlined procurement processes.
Recording & Update:
In a procurement system, the recording and updating of storage location master data can be done manually or through synchronisation with the inventory system.
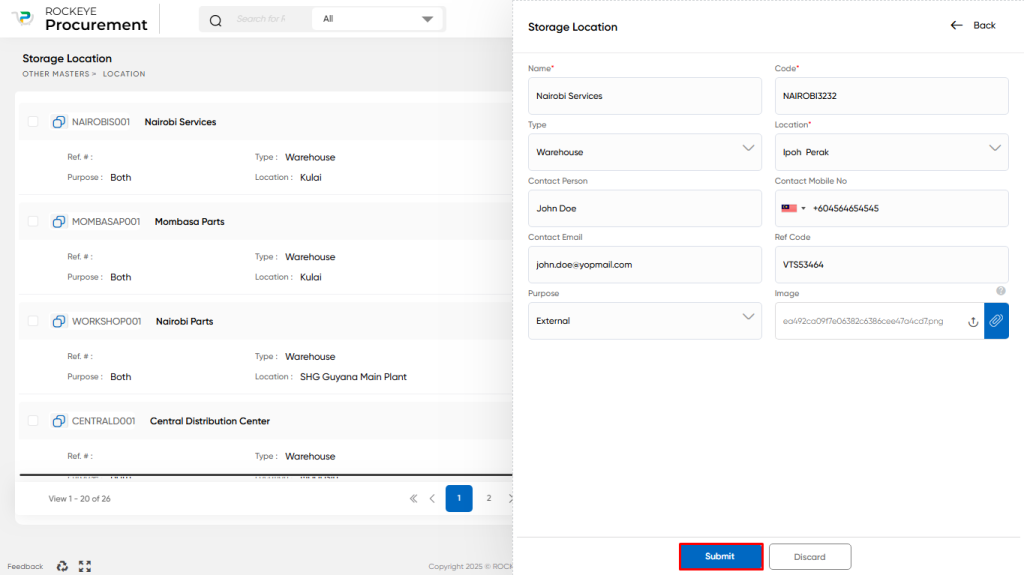
Here are the details regarding the fields required for the manual creation and update of storage location records:
- Name: This field captures the name of the storage location. It is a unique identifier used to distinguish one storage location from another.
- Code: The code field provides a unique alphanumeric code that represents the storage location. It helps in easy identification and reference of the storage location.
- Type: The storage location type indicates the category or classification of the storage location. Examples include Warehouse, Plant, Project, or User Department. This field helps in organising and categorising the storage locations based on their purpose or function.
- Location: This field is a dropdown list that allows the selection of the physical location from a predefined list of locations available in the location master. It ensures consistency and accuracy in recording the storage location’s specific address or coordinates.
- Contact Person Details: These details include the name, mobile number, and email address of the designated contact person responsible for the storage location. This information is useful for communication and coordination purposes.
- Reference Code: The reference code field is an optional field that can be used to link or associate the storage location with any other relevant code or identifier in the system. It helps establish connections or relationships between different entities within the procurement system.
- Purpose: This field captures the purpose of the storage location, such as Internal, External, or Both. It specifies whether the storage location is intended for internal use within the organization, external use for customers or suppliers, or both.
- Image: This optional field allows users to upload an image or visual representation of the storage location. It can be useful for visual reference or identification purposes.
If an approval flow is enabled in the procurement system, any new storage location records or updates to existing records may undergo an approval process before they are finalised and become active in the system.
By recording and updating the storage location master data in the procurement system, organisations can maintain accurate and detailed information about their storage locations, enabling efficient inventory management, streamlined procurement processes, and effective decision-making.
The user can perform the following actions in this section:
- Submit: This option allows the user to publish the transaction information. If the system has an approval flow, the maker will submit the information, and it will be sent to the approval authority or checker for approval.
- Discard:
This option allows the user to discard the transaction before saving it.
Key Notes Storage Location:
- Storage locations are usually synced with the INVENTORY system if integrated, accomplished by selecting “Sync Bank List” from the Storage Location listing.